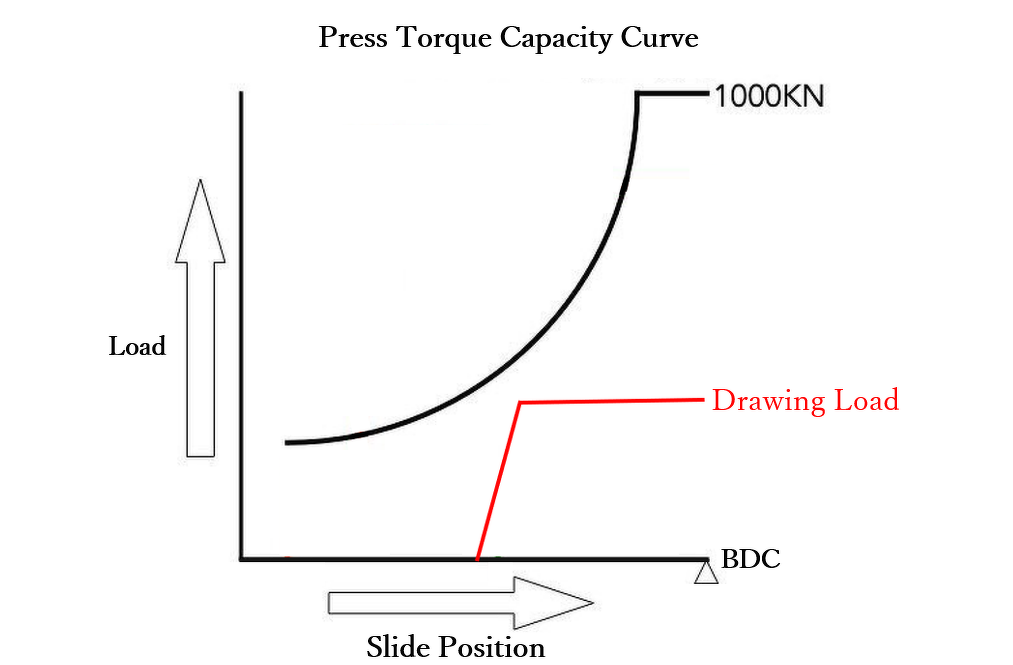
Draw-Forming (Part 3): How to Determine the Optimal Press Capacity
In Parts 1 and 2 of this series, we discussed the 'wrinkling suppression force' necessary to suppress wrinkling and cracking when draw-forming and how to calculate the 'appropriate number of draws.'
In Part 3 (the final part) of this series, we will discuss how to determine the optimal press capacity.
In order to select a press to perform draw-forming, you must first calculate the "required draw-forming force" and the "required working energy."
How to Select the Appropriate Press
Once the process layout has been decided, the press model is selected by taking into consideration the three press capabilities - pressure capacity, torque capacity, and work capacity.
For draw-forming, the force and working energy required for the process must be calculated, and a press machine with a capacity that exceeds the calculated value must be selected.
How to Calculate the Force and Working Energy for Cylindrical Draw-Forming
We will explain the calculation method for the draw-forming of a cylinder, which is a typical drawn shape.
[The Force Required for Cylindrical Draw-Forming]
The following equation is commonly used to calculate the force required for cylindrical draw-forming.
Pd=π×dp×t×σb÷1000
Pd: The force required for cylindrical draw-forming (kN)
dp: Punch diameter (mm)
t: Material thickness (mm)
σb: The tensile strength (N/mm²) of the material being formed Note: See Table 3
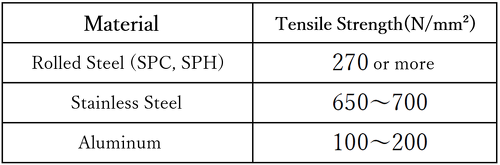
Table 3: Tensile Strengths of Various Materials
[The Working Energy Required for Cylindrical Draw-Forming]
The following equation is used to calculate the working energy.
Ed=(Pd+Pad)×hd×Cd
Ed: The working energy required for cylindrical draw-forming (J)
Pd: The force required for cylindrical draw-forming (kN)
Pad: The wrinkling suppression force
hd: Drawing depth (mm)
Cd: The coefficient given in Table 4

Table 4: Coefficient 'Cd' for the Working Energy Required for Cylindrical Draw-Forming
Let's Give It a Try!
(Problem)
Let's calculate the force and working energy required to draw-form a product with an I.D. of 116* using a blank with a diameter of φ200.
* Assume that the material is 2 mm-thick SUS (stainless steel), the drawing depth is 20 mm, and the drawing die radius is R6.
* Because the sheet thickness is 2 mm, the die I.D. will be the following: 116+(t2×2)=φ120.
(Answer) (π=3.14)
① Force Required for Draw-Forming (when assuming σb=700)
Pd=π×dp×t×σb÷1000=π×116×2×700÷1000=510 kN (rounded)
② Wrinkling Suppression Force
Since Pad=An×pb÷1000, Pad=17722×4÷1000=71 kN (rounded)
(For information about the wrinkling suppression force, see "Draw-Forming (Part 1): How Do You Calculate the Optimal Wrinkling Suppression Force?")
③ The Working Energy Required for Cylindrical Draw-Forming]
Drawing Rate: Since 116÷200=0.58, we will use 0.77 for coefficient Cd.
Ed=(Pd+Pad)×hd×Cd=581×20×0.77=8947 (J) (rounded)
In other words, a press* with a pressure capacity of 581 kN or higher, a torque capacity of 581 kN or higher at 20 mm above bottom dead center, and a working energy of 8947 (J) or higher could draw-form this product.
Looking at AIDA's press lineup, in the case of intermittent operation an NC1-1100(2) has the requisite working energy to form the product, but its torque capacity is insufficient. When factoring in torque capacity, the optimal press would be an NC1-1500(2).
(*Please contact an AIDA representative for models with catalogs that do not list the working energy and/or torque capacity.)
Did you find this helpful?
We have now covered the subject of draw-forming in 3 parts, where we discussed how to calculate the optimal 'wrinkling suppression force,' the 'number of draws,' and the 'press capacity.'
Please do not hesitate to contact AIDA if you have any questions.