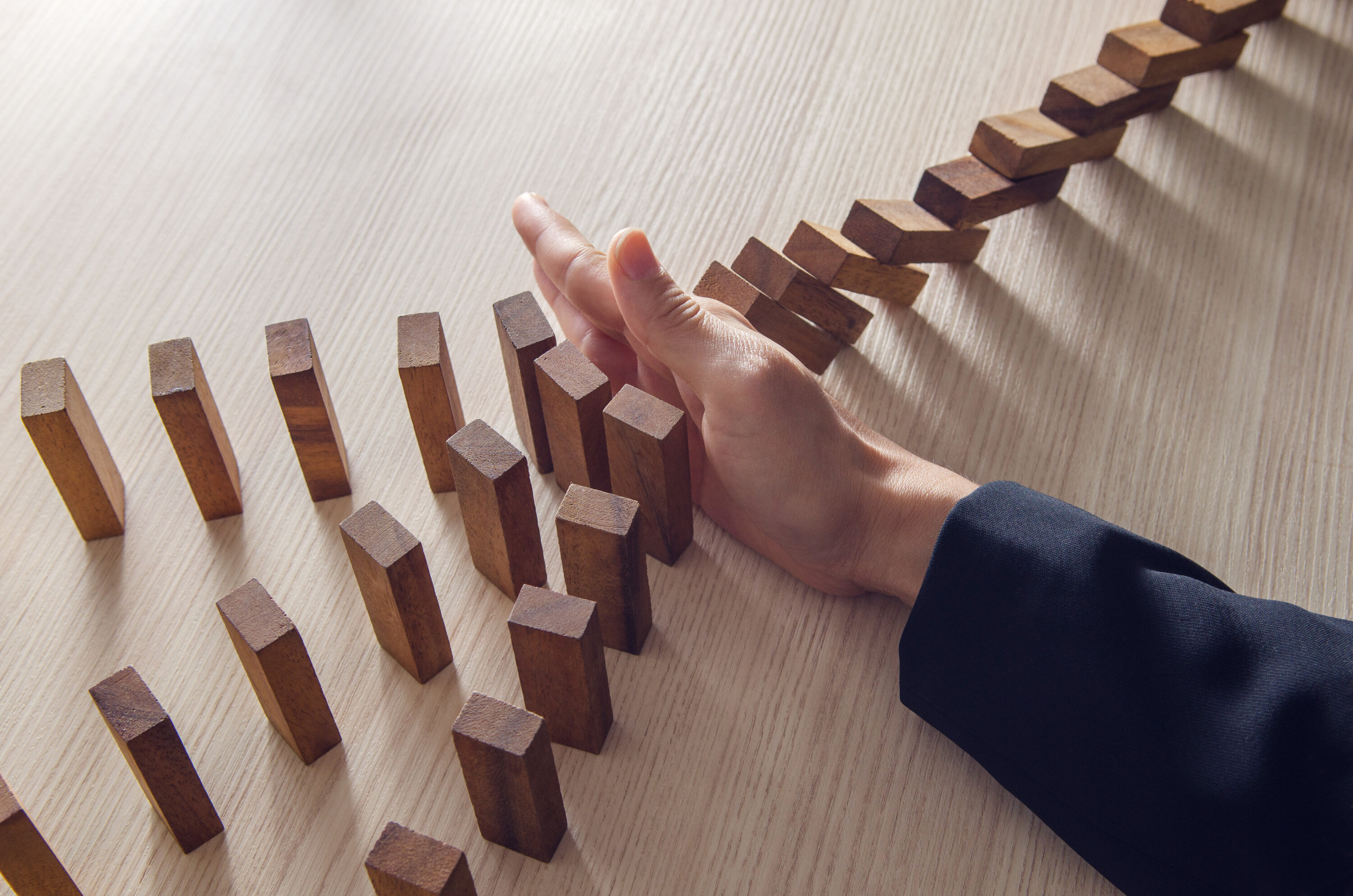
What is the "Allowable Intermittent SPM"?
Have you ever heard the term 'Allowable Intermittent SPM'?
The allowable intermittent SPM specification is the number of strokes a press is capable of performing in one minute when it is being used for intermittent operation.
Intermittent operation is defined as a press operation where the press starts and moves the slide for one cycle before stopping at the preset stop position. Then, after a specific amount of time has elapsed, the press will repeat this one-cycle stroking-and-stopping sequence.
Intermittent Operation Applications
Intermittent operation is used on tandem lines and robot lines, etc., in cases where it is necessary to stop the press (the press slide) for a specific period to allow time for material to be inserted or to transfer or remove products.
In the case of transfer press lines and progressive press lines where forming is done with the press running continuously, in many cases the press will not have an allowable intermittent SPM specification (i.e., it is not designed to be run intermittently.
How the Allowable Intermittent SPM Specification is Expressed
The allowable intermittent SPM specification is often expressed as '15 at 30 min-1.'
This means that the slide speed (the no-load continuous SPM) is set at 30 min-1, and that the press is limited to 15 strokes per minute.
As shown below, one operation cycle will be 4 seconds (60/15=4), and because the slide speed is 30 min-1, this means that the press slide will run for 2 seconds, then stop for 2 seconds, and then will continue to repeat this same cycle.


A Sample Diagram (The curve shows the allowable limits)
How the Allowable Intermittent SPM is Determined
The intermittent SPM performance of the press is determined by the press specifications (the stroke length, the continuous SPM value, the slide motion, the slide weight, etc.) in combination with the brake capacity.
The brake capacity is especially important in determining the allowable intermittent SPM. Specifically, the allowable intermittent SPM is determined based on the brake's capacity to absorb the energy required to stop the slide (stopping performance) and on its cooling (heat dissipation) capacity in relation to the heat that is generated when stopping the slide.
Note: If the generated heat is not fully dissipated after each stroke, the brake temperature will slowly increase, and this could possibly degrade stopping performance or cause other issues due to the amount of generated heat.
In general, the faster the slide speed, the greater the heat generation will be during stopping, which means that the press will be stopped at the preset stop position for a longer period of time (the cooling time), and this results in a lower allowable intermittent SPM (number of intermittent strokes).
A Final Note
The reality is that the appropriate intermittent SPM will be determined by the performance of the press coupled with the performance of the peripheral equipment (loaders, unloaders, etc.), and thus it is not necessarily the case that the press will always be running at its maximum allowable intermittent SPM (its maximum capacity value).