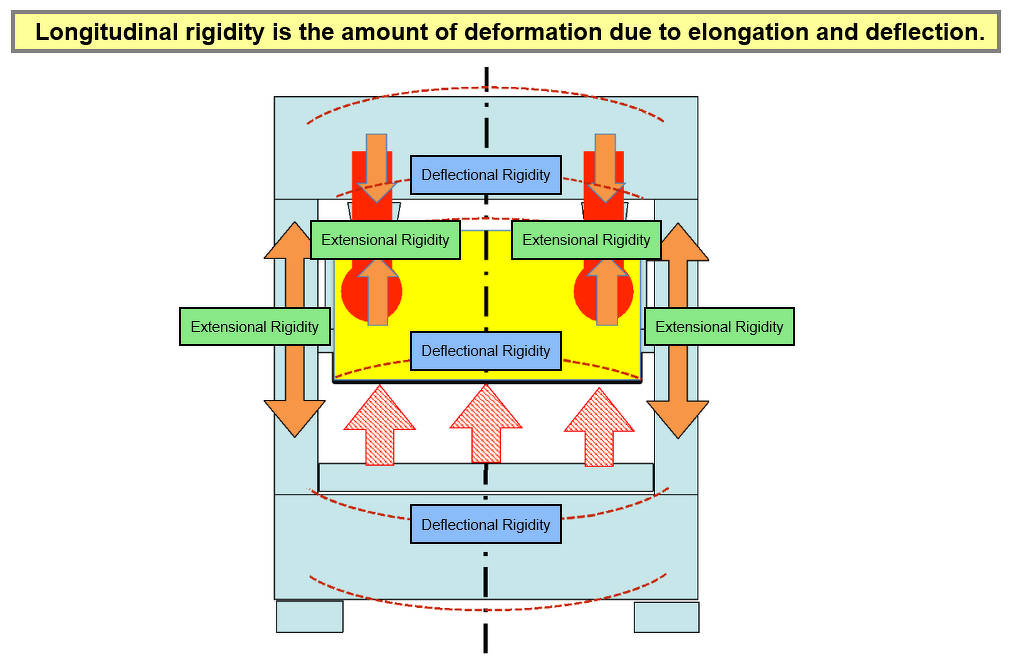
What is Press Rigidity?
When defects are found in press-formed products and other issues such as noise and vibration occur, you have perhaps heard someone comment, 'I don't think this press is rigid.'
There are also different types of press rigidity, so this post will explain the differences between them.
Broadly speaking, there are two types of press rigidity--longitudinal rigidity and lateral rigidity. Most discussions about rigidity involve longitudinal rigidity.
■ What is Longitudinal Rigidity?
Longitudinal rigidity is the general term given to rigidity in the longitudinal (vertical) direction of the press, and it is primarily expressed as the amount of deformation due to "extensional rigidity" (the amount of press elongation) and "deflectional rigidity" (the amount of slide and bed deflection) when a forming load is applied on the press. As press longitudinal rigidity increases, the amount of deformation will decrease.
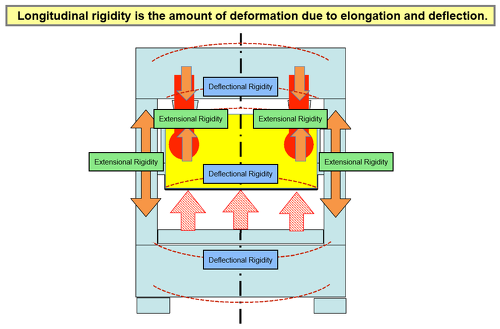
Extensional Rigidity
The amount of extensional rigidity is evaluated based on the amount of elongation of each frame member and the amount of contraction of the pressure-receiving drivetrain areas when a forming load is applied on the press. This is usually checked by using a hydraulic jack, etc., to apply a specific load on the press and then measuring the distance between the slide and bolster.
Deflectional Rigidity
The amount of deflectional rigidity is evaluated based on the amount of slide and bed deflection when a forming load is applied on the press. This is usually expressed as the amount of deflection when a uniformly distributed load is applied to 2/3rds of the specification area. Deflectional rigidity is expressed as a value, such as "1/10,000." The means that when a load equal to the maximum rated capacity of the press is applied to a bolster with a left-right dimension (the measurement range) of 3000 mm, that the difference in the amount of deflection at the left and right edges of the bolster compared to the center would be 0.3 mm (in other words, 1/10,000th of 3000 mm).
If the deflectional rigidity value is half of that--i.e., 1/5,000--the amount of deflection would be twice as large at 0.6 mm. Each press manufacturer defines the load conditions when measuring this as well as the measurement methods.
■ What is Lateral Rigidity?
Lateral rigidity is the rigidity in relation to lateral (horizontal) loads that occur due to off-center loads, etc.
Ways to increase rigidity include strengthening the slide gib structure and increasing the number of slide pressure-receiving points from 1 to 2 or 4 points, and can also include spacing the slide points wider apart as a countermeasure to reduce the adverse effects of off-center loads.
In contrast to longitudinal rigidity, it is usually quite difficult to evaluate lateral rigidity quantitatively, and thus it is almost always evaluated in terms of product accuracy under actual forming conditions.
■ The Relationship Between Rigidity and Product Accuracy
Why do product dimensional fluctuations increase so much when products are formed using a low-rigidity press?
During actual continuous press operation, the forming loads that are applied during each stroke are not uniform--they will fluctuate due to various factors, such as the material thickness, the volume of the slug, the deformation resistance value of the material, the press lubrication conditions, a rise in the temperature of the press, and die wear, etc. These load fluctuations greatly influence the amount of press deformation.
Assuming that the load variations are falling within the same ranges, a low-rigidity press (blue) will experience a large amount of deformation and a high-rigidity press (red) will experience a small amount of deformation.
This is why there are such large product dimensional fluctuations when using a low-rigidity press.

■ A Final Word....
Press rigidity is a very important factor in product accuracy.
If you want to minimize dimensional variations in your products when performing high-precision forming, etc., it is important to either select a high-rigidity press or select a press with sufficient excess capacity with respect to the required forming load.