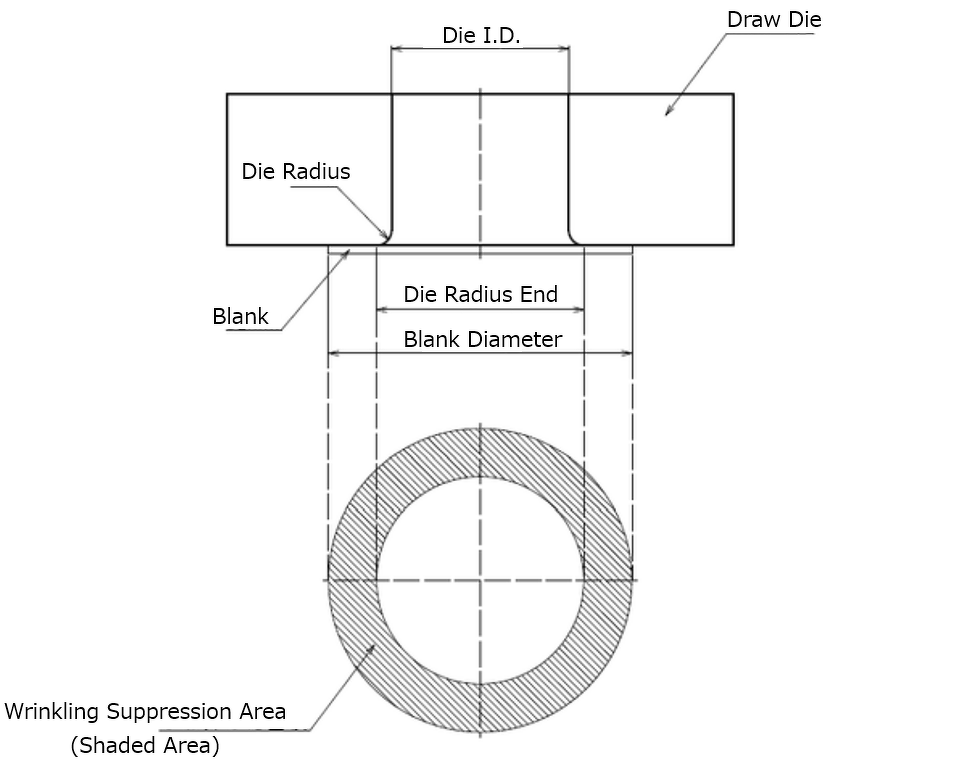
Draw-Forming (Part 1): How Do You Calculate the Optimal Wrinkling Suppression Force?
In this 3-part series we will be discussing 'draw-forming.'
Drawforming is a methodology that can produce seamless, beautifully formed products, but it is very important to do calculations beforehand in order to set the correct forming conditions. In Part 1 we will discuss how to calculate the 'wrinkling suppression force.'
What is Draw-Forming?
Drawing-forming is a technique for forming sheets into seamless bottomed shapes such as cylinders or square tubes.
Since the final shape is achieved without additional processes such as machining or welding, productivity is high and this is a major advantage that is unique to press metalforming, but if it is done incorrectly, the final products can be defective due to wrinkling and cracking, etc. It is therefore necessary to implement countermeasures for wrinkling and cracking in advance.
What is the Wrinkling Suppression Force?
Wrinkling occurs at the time the blank is drawn down into the drawing die. Accordingly, the blank must be held securely in place by the die to prevent wrinkling. If the holding force is too weak it will result in wrinkling; if the holding force is too strong, the blank material will not be sufficiently drawn into the die and it will result in cracks.
Therefore, the optimal wrinkling suppression force is the minimum force required to eliminate wrinkling. The wrinkling suppression force will vary depending on the material and the area that is being held in place, but it is possible to calculate an approximate value.
[How to Calculate the Wrinkling Suppression Force]
Pab=An×pb÷1000
Pab: The wrinkling suppression force (kN) for cylindrical draw-forming
An: The area (mm²) of the wrinkling suppressor that holds the blank down.
pb: Holding Surface Pressure (N/mm²)
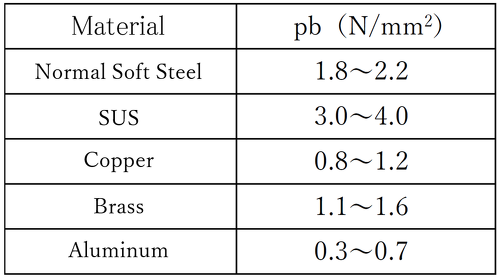
Table 1: pb Values for the Draw-Forming Limit
Let's Give It a Try!
Let's try calculating the optimal wrinkling suppression force.
[Problem]
What would the wrinkling suppression force (kN) be when draw-forming a blank with a diameter of φ60 into a drawing die with an I.D. of φ34?
We will assume that the material is 1 mm-thick regular soft steel and that the drawing die radius is R3.
Note: The area of the blank holder that holds the blank is the blank area minus the area of the diameter of the die radius end of the drawing die.
Note: R is the radius, and 2R is the diameter. Accordingly, R3 has a radius of 3 mm. The diameter of the drawing die radius end is the sum of the I.D. of the die and twice the die radius (i.e., the diameter). Accordingly, the 'Die Radius End' diameter = Die I.D.+2R
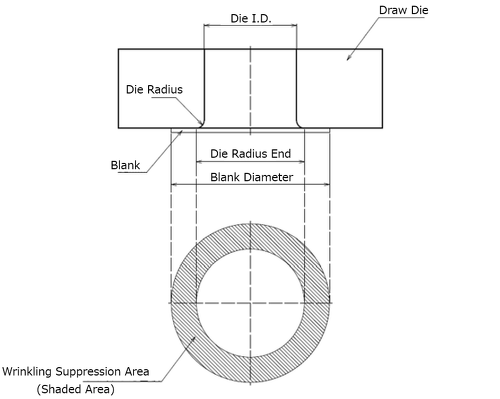
Drawing Die Diagram
[Equations] (π=3.14)
1. Blank Area
If the blank radius is R, then the blank area=πR², and thus the area of the blank diameter is as follows: V₁=π×30²=2,826 mm²
2. The Area of the Die Radius End Diameter
If the radius of the die radius end is r, then r=Die I.D.÷2+3, and thus =17+3=20 mm
The Die Radius End radius area V₂: Since the area =πr², V₂=π×20²=1,256 mm²
3. Wrinkling Suppression Area (An)
An=V¹-V²=2,826-1,256=1,570 mm²
4. Wrinkling Suppression Force
When pb=1.8 N/mm², Pab=1,570×1.8÷1000=2.83 kN (rounded)
(Answer)
2.83 kN
Did you find this helpful?
In Part 2 of this series, we will explain the 'drawing rate' in detail. We hope you will take the time to read it!