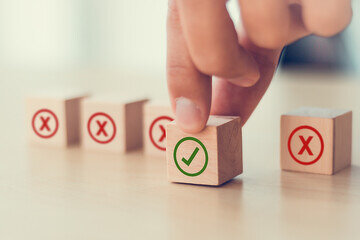
Considering Forming Loads When Selecting a Press
This article covers the topic of press forming loads at it relates to the selection of a press.
In order to form a product that requires 1000 kN (100 tons) of pressure, it necessitates a press with a rated capacity of 1000 kN or higher.
As you can understand, it is not possible to form something requiring 1000 kN using a press with a capacity that is less than 1000 kN (it won't make a good product), and in a worst-case scenario it could cause heavy damage to the press.
In order to avoid a situation like this, the general recommendation is to use a press where the forming load will not exceed approximately 70% of the nominal capacity of the press.
The reason for this is that there may be load variations during mass production or setting errors that could increase the forming load, etc.
And in the case of blanking with its accompanying fracturing of the metal, after factoring in the effects of breakthrough--where the slide will suddenly plunge downwards when the load abruptly drops to zero when blanking is completed--the recommendation is to use a press at 50~60% of its nominal capacity.
However, it is not always the case that the forming load will always be applied at bottom dead center.
Depending on the type of forming, the load may be applied at some other position.
The following illustrations show the relationship between the slide position and the load for a number of typical forming methods.

Fig. 1: The Relationship Between Slide Position and Load When Blanking

Fig. 2: The Relationship Between Slide Position and Load When Bend-Forming

Fig. 3: The Relationship Between Slide Position and Load When Extruding

Fig. 4: The Relationship Between Slide Position and Load When Draw-Forming

Fig. 5: The Relationship Between Slide Position and Load When Squeezing
As shown in the 5 illustrations above, the slide position where the maximum load will be exerted will vary greatly depending on the forming method.
in the case of a mechanical press, the slide position above bottom dead center where load can be applied will vary due to differences in the torque capacity (one of "The 3 Elements of Press Capacity"), and thus when selecting a press it is necessary to understand at what position the maximum load will occur.
Figure 6 below is a graph that shows the torque capacity of a 1000 kN press when bend-forming and when draw-forming with a 800 kN forming load.

Fig. 6: Press Torque Capacity When Bend-Forming and Draw-Forming
In the example shown in Fig. 6 above, in the case of bend-forming, it is possible to use a 1000 kN press because the load falls within the torque capacity curve.
In the case of draw-forming, a 1000 kN press does not have sufficient capacity because the load would extend beyond the torque capacity curve. It will be necessary to use a higher-capacity press.
And in cases where forming is done at a position that is high above bottom dead center, it is also necessary to verify the working energy ("The 3 Elements of Press Capacity: Work Capacity").
We will explain the torque capacity and the work capacity (2 of "The 3 Elements of Press Capacity) separately.