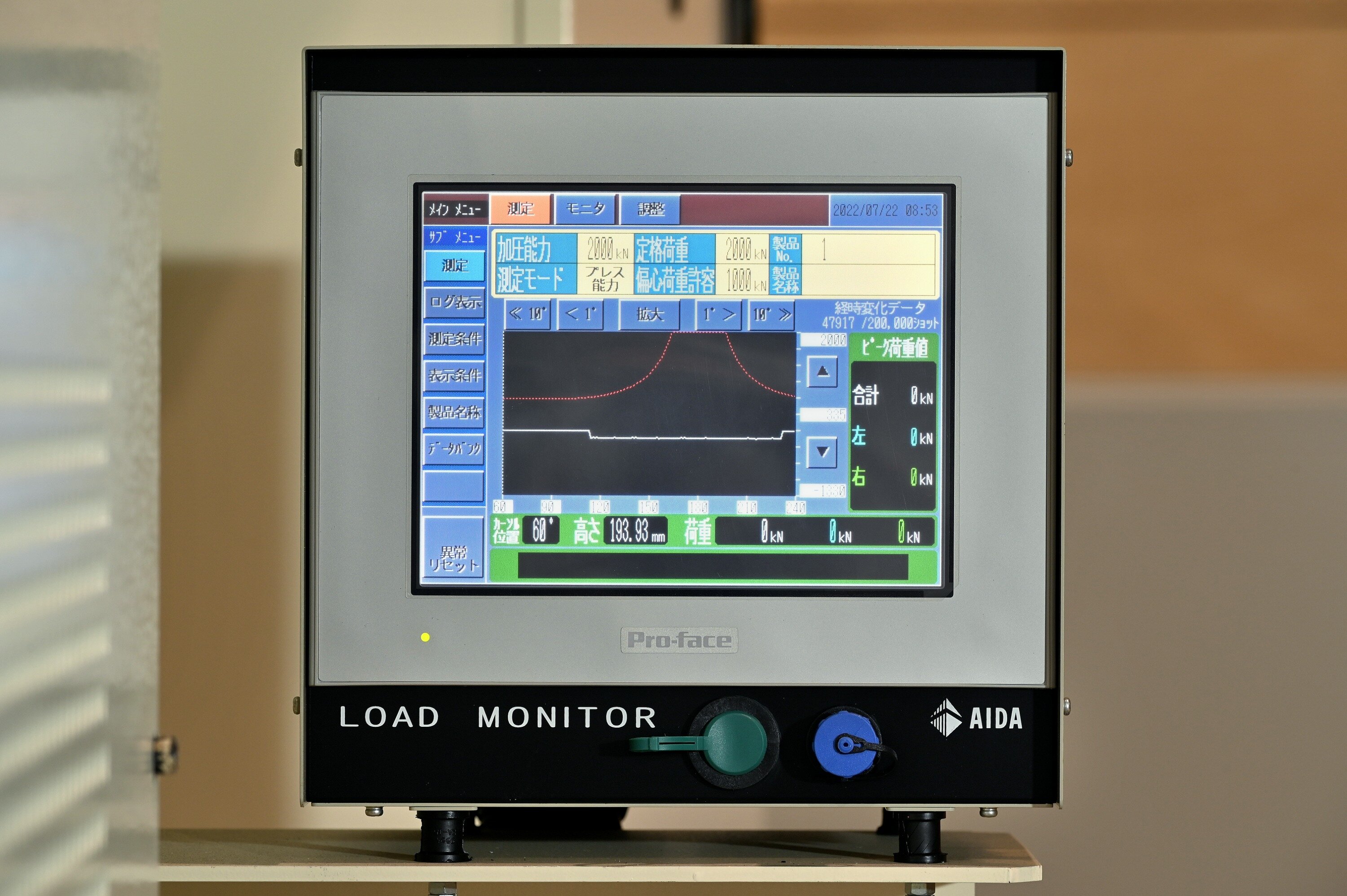
What Does a Load Monitor Do?
Presses form products by exerting the necessary load on material via the dies. If the load is not transmitted appropriately, it can result in defective products and cause die damage. In this post we will discuss load monitors, which are often used with presses. Although the primary purpose of a load monitor is to display the forming load values while the press is forming products, it also functions as a device that notifies the user of material, die and press issues.
It is certainly important for a load monitor to display the total forming load (peak load), but notifying users of load value variations enables users to discover material variations (thickness, hardness, etc.) and die and press abnormalities (damage), and it also enables users to quickly discover product forming defects.
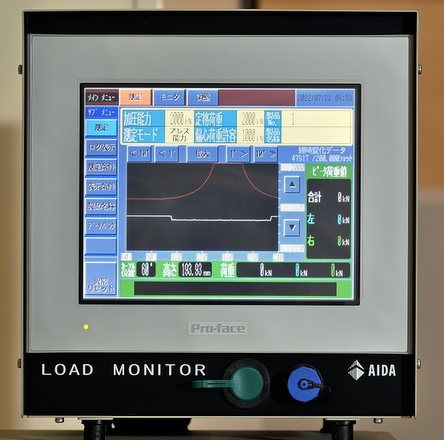
AIDA's ALA3 Load Monitor
Do Displayed Load Values Differ Depending on the Press?
Even if using the same dies to form products, changing the press can also change the displayed load values.
The primary reasons for this are as follow:
① Differences in the shape of the press frames and the mounting locations of the strain gauges used to detect load. (Different load transmission paths)
② Differences in press frame extensional rigidity and/or slide and bed deflectional rigidity.
(If the rigidity is different, the forming load values will differ even if the same die is used at the same die height.)
③ Differences in the load detection medium, such as strain gauges vs. hydraulic pressure.
(Hydraulic pressure-type detection is used to directly detect pressure fluctuations inside the overload safety device, so it has higher measurement accuracy than strain gauge-type detection, which measures displacement on the frame surface.)
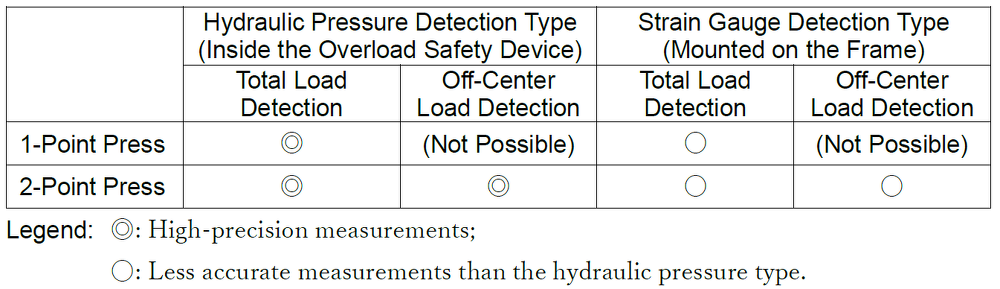
Load Monitor Interlock Functions
An interlock is a method for controlling a function so that it will not be activated unless multiple predetermined conditions are met.
AIDA's load monitor (ALA-model Graphic Load Analyzer) is equipped with the following interlocks to respond to detected load values.
① If the measured load value exceeds the press stroke pressure curve (torque capacity), continuous press operation will be halted.
② If the value of the loads being applied on the suspension point[s] exceeds the capacity of the point[s], continuous press operation will be halted.
③ If the load difference between the right and left suspension points exceeds the setting value, continuous press operation will be halted.
(This protects the press and the dies by limiting slide tilt caused by off-center loads.)
④ If a fluctuation range is set for a specific load trend and that range is exceeded, press operation will be halted.
Automatically stopping the press when the above conditions occur will protect the press and the dies and enable the detection of defective formed products at an early stage.
Evolving Load Monitoring Systems
Furthermore, load monitoring systems that provide greater visibility by using load monitor data have recently been introduced. These systems display load trends for the entire bolster as a 3D graph, enabling users to see load waveform anomalies and the position where the maximum load is being applied at a glance, enabling quick responses to issues.
(The graph below was generated by AIDA's Ai CARE Data Analytics System. For two-point presses only.)
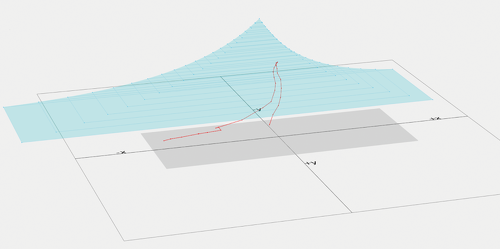
The Load Trends for the Entire Bolster Can be Displayed as a 3D Graph (Two-Point Presses Only)
Did you find this helpful?
Please do not hesitate to contact AIDA if you have any questions.