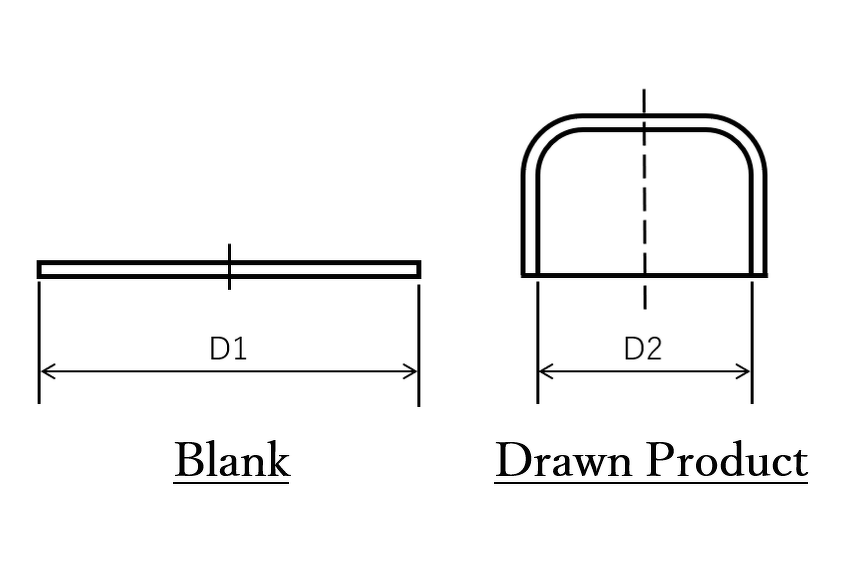
Draw-Forming (Part 2): How Do You Calculate the Appropriate Number of Draws?
In Part 1 of this series we discussed the 'wrinkling suppression force' necessary to suppress wrinkling and cracking when draw-forming.
Draw-forming is a methodology that can produce seamless, beautifully formed products, but it is very important to do calculations beforehand in order to set the correct forming conditions.
In Part 2 of this series we will be discussing the 'appropriate number of draws.'
What is the Drawing Rate?
When draw-forming cylinders, there is a limit to the diameter of what can be drawn at one time.
The 'ratio of the diameter before and after drawing' is called the 'drawing rate,' and it is a value that is used as a guideline for the drawing limit.
Put another way, if D1 is the blank diameter and D2 is the draw-formed diameter, the drawing rate is D2÷D1.
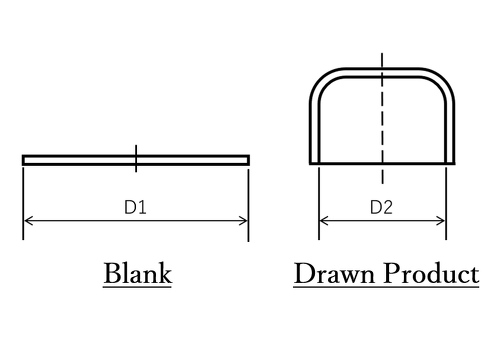
If a process is designed without factoring in the drawing rate, the material can crack while it is being drawn.
The following measures can be taken to prevent this.
1) Factor in the drawing rate when designing the forming process.
2) Based on the number of times the product is redrawn (the 2nd and subsequent draws), use settings that gradually loosen the drawing rate (make the values given in the standards in "Table: The Drawing Rate Limit for Each Type of Material" larger).
The Process Layout Design Procedure
1) First, calculate the volume of the final product. When calculating this, you must also include the volume of the scrap from piercing and trimming.
2) Next, use the calculated volume to calculate the blank diameter that would match it.
3) Once the blank diameter is determined, determine the number of draws while referencing the following: 'Table: The Drawing Rate Limit for Each Type of Material.'
If piercing or trimming is required, this is usually done after the draw-forming.
Let's Give It a Try!
(Problem)
How many draws are required to draw-form a product with an I.D. of φ22.5 from a blank with a diameter of φ60.
Assume that the material is a deep-drawing steel.
Because the final shape cannot be attained through only a single draw, draw-forming must be repeated a number of times. As explained above, use settings that gradually loosen the drawing rate based on the number of redraws.
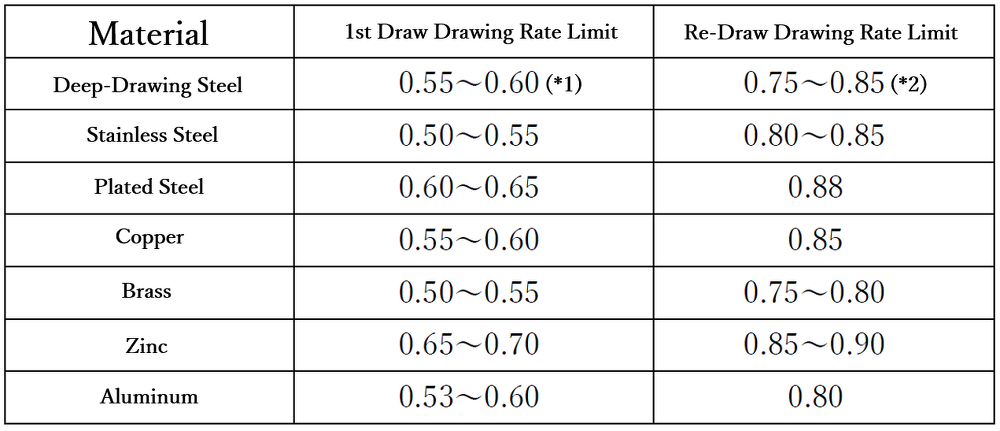
Table: The Drawing Rate Limit for Each Type of Material
(Answer)
If the drawing rate of the first draw is 0.55 (see Note 1 in the above Table), then D2=φ60×0.55=φ33.
If the drawing rate of the second draw is 0.80 (see Note 2 in the above Table), then D3=φ33×0.80=φ26.4
The third draw will result in the final target product inner diameter of φ22.5 (φ22.5÷φ26.4 = 0.85), and since 0.85 is within the criteria in Note 2 in the above table, we can see that it is possible to reach the target product diameter during the third draw.
Accordingly, it will take 3 draws to form the product.
Did you find this helpful?
In Part 3 (the final part) of this series, we will discuss "How to Determine the Optimal Press Capacity." We hope you will take the time to read it!