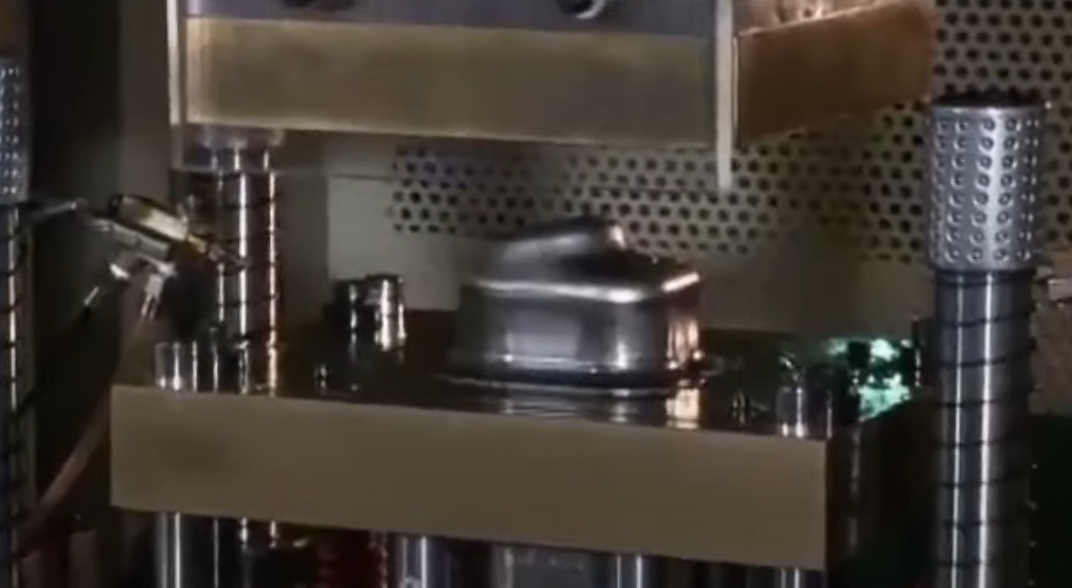
Frequently Asked Questions ~Metalworking Lubricants for Presses~
In this blog post, we will use a Q&A format to discuss frequently asked questions about metalworking lubricants. We also recommend this section for new learners!
Q1: What are press metalworking lubricants?
A1: Press metalforming is the process of forming a material into the shape of a die by placing material between an upper and lower die and applying heavy pressure. Because the material is formed by being forcefully pressed against the die, depending on the forming application, the dies and workpieces may become scratched and/or workpieces may crack due to friction, or seizing may occur due to friction-induced heat. Accordingly, press metalworking lubricants are used for many press metalforming applications, where the lubricant is applied to the surface of the material or to the die surfaces to create an oil film on the metallic surfaces that serves to reduce friction, thereby protecting dies and workpieces from scratches and from cracking issues. Press metalworking lubricant types include oil-based lubricants, water-soluble lubricants, dry lubricant films, and plastic films, and the type that is used varies depending on the application.

There are many different types of press metalworking lubricants to choose from to match the workpiece material, the metalforming method, and other performance requirements. Metalworking lubricants can be broadly divided into water-insoluble (oil-based) types, water-soluble types, and solid lubricant dispersion types. For each type, a base material is selected and the amount of additives is adjusted to meet secondary performance and environmental performance requirements.
Q2: What are some environmental countermeasures that relate to press metalworking lubricants?
A2: It is necessary to take into consideration the environment when it comes to the usage and disposal of not only the press metalworking lubricants but also the product cleaning fluids (solvents) used after the press metalforming process. Depending on the usage, press metalworking lubricants may include a wide variety of chemical substances (additives), but one needs to be especially careful with metalworking lubricants that contain chlorine-based extreme pressure additives.
Chlorine-based extreme pressure additives provide superior seizing prevention performance, and thus they have been used in a wide variety of metalworking lubricants aside from press metalworking lubricants, but concerns have been raised regarding the possible release of dioxins during the post-disposal incineration process. And the cleaning fluids (solvents) that are used after the press metalforming process may contain substances that destroy the ozone layer. As a result, in recent years non-chlorinated metalworking lubricants with special friction-reducing blended additive and quick-drying or volatile metalworking lubricants that eliminate or reduce cleaning after the press metalforming process are being recommended.
Q3: We are using a chlorine-based oil for the multi-stage draw-forming of a cylindrical product (a motor housing) from 4.5 mm-thick SPCC, but we are having problems with rust forming on the sides of the draw-formed walls. Is there some metalworking lubricant that would help us resolve this issue?
A3: Chlorine-based metalworking lubricants are more likely to cause rust because of chemical reactions due to the chlorine.
Press metalworking lubricant G-3641 (Mfr.: NIHON KOHSAKUYU CO,. LTD.) is a non-chlorinated oil that inhibits rust and its draw-forming performance is equivalent to that of chlorine-based oils. By changing to this oil, rust on draw-formed walls was completely eliminated without impairing formability, and the defect rate dropped significantly.
Q4: We are using non-chlorinated oils for the progressive blanking and ironing/bending of 0.5 mm-thick SUS304 material, but because it is sticky, we have problems such as scrap sticking in the dies and the dies getting grimy. Is there some way to improve the current situation?
A4: Non-chlorinated press metalworking lubricant G-3008D (Mfr.: NIHON KOHSAKUYU CO,. LTD.) is a low-viscosity metalworking lubricant that uses a unique blend of additives to maintain the same performance as conventional metalworking lubricants. Changing to this lower-viscosity oil solved the problem of scrap sticking to dies, and it also reduced the amount of grime on the dies, which greatly improved their work efficiencies.
Q5: We are using a drying-type oil for the progressive drawing of 1.0 mm-thick SECC material and also for blanking (air-bag parts), but during the summer this tends to dry too fast, which degrades its lubrication performance. Are there any countermeasures for this?
A5: G-6376F (Mfr.: NIHON KOHSAKUYU CO,. LTD.) has a long drying time, and it will remain on products without drying until the next process. Not only does this extend the life of your dies, its smell while drying has also been improved. However, a small amount of oil will remain even after it has dried.
Q6. What are the effects of press metalworking lubricants on the press itself?
A6: Though there is no industry literature about the effects of press metalworking lubricants on presses, there is a long history of statements regarding its effects on resins and rubber, such as paint and packing/seals, and it has been verified that shape changes occur when resins and rubber come into contact with lubricant elements. Based on experience, it is believed that the higher the compatibility is between a lubricant's elements and the resin elements, the more likely it is that such changes will occur. Polycarbonates and acrylic rubbers have low oil resistance properties and they may expand or turn white if oil adheres to them. And though polycarbonates are used for press safety guards because of their superior impact resistance properties, they sometimes crack when oil-based fluids adhere to them and they then come into contact with press-formed parts or scrap.
Q7: Are there any things to be careful about when using water-soluble die lubricants as press metalworking lubricants?
A7: If water-soluble metalworking lubricants contaminate press and auxiliary equipment lubricating oils, it can degrade these lubricating oils and cause the press to generate heat during operation, which could cause major issues such as galling. Moreover, it can result in rusting and shorten the service life of the equipment. When using water-soluble metalworking lubricants, it is necessary to implement countermeasures such as limiting the usage amounts and adding an oil/water separator unit.
.png)
Rusting Due to Contamination by a Water-Soluble Metalworking Lubricant
.jpg)
One Example of a Oil/Water Separator Unit
Q8: What methods are used to apply metalworking lubricants on sheet materials?
A8: Aside from manually brushing and spraying it on, the three most common methods are listed below.
① Drip Type
② Oiling Roller Type
③ Automatic Spray Gun Type
Each of the above methods has advantages and disadvantages, so it is important to select the method that fits your press metalforming conditions.
Did you find this helpful?
Questions 3~5 were written with the cooperation of NIHON KOHSAKUYU CO,. LTD.
For more information about the selection of metalforming lubricant types, environmental measures, and other topics, please contact a dedicated lubricant manufacturer.
Our next blog post will discuss "Press Lubricants."
We hope you will take the time to read it!