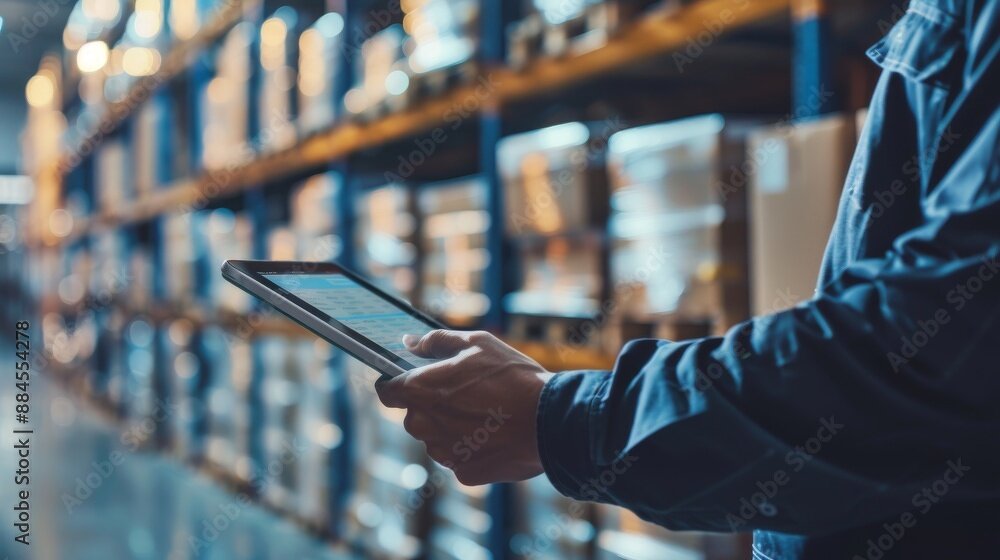
What Spare Parts Should We Keep on Hand?
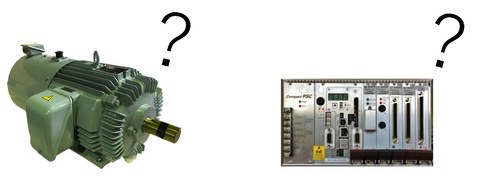
Spare Parts image
Have you ever had a press stop running and, as you are frantically looking for a replacement part, you are shocked to learn that it has a very long lead time?
Here's some advice to avoid such a predicament.
The availability of the various components purchased from parts manufacturers differs significantly depending on whether the parts are mass-produced or made-to-order.
For example, if a 7.5 kW and a 90 kW motor are used in different locations on your equipment, even if the motor manufacturer is the same, the small motor will be more readily available in the market because it is a general-purpose model. On the other hand, midsize and large motors are generally made to order and are almost impossible to find in the open market.
You can keep production line downtime to a minimum by planning to keep such spares in stock.
Please also keep in mind that even if the manufacturer's model designation appears to be that of a generic model, it might also be a special-order item because the press manufacturer has requested some degree of customization.
For example, in some cases the specifications of two products will be identical, but there may be an extra letter, etc., at the end of the model designation for one of the products because the orientation and the dimensions of an attached connector have been customized, so you need to take care to check for such things very carefully.
In terms of both cost and management, it is not realistic for customers to keep every single replacement part in stock. However, in order to not panic when a replacement part is urgently needed, for parts not kept in stock it is important to have a clear understanding of the lead times, estimated costs, usage locations, and usage quantities, etc.