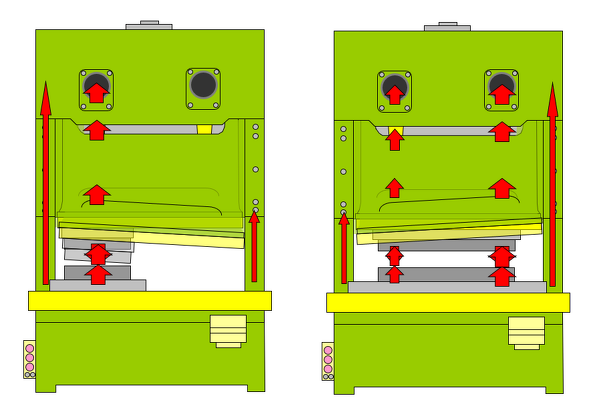
Allowable Off-Center Load Diagrams--Part ①
Press-made products--which range from high-precision connectors to vehicle outer panels--are formed using a variety of metalforming methodologies and a wide array of die types.
Because of this, there are times when the center of the forming load being applied on the press is near the center of the press as well as times when it isn't (this is referred to as 'off-center loading').
In cases where the center of the forming load is approximately the same as the press center, it is a good practice to make sure that the total forming load does not exceed the press capacity, but if the center of the forming load is some distance from the press center (i.e., the load is off-centered), depending on the characteristics of the press being used, it can result in limitations to the total forming load even if the load is below the rated capacity of the press.
Generally speaking, forming loads are more often off-centered than not, and an Off-Center Load Diagram is used to show the forming load limits under such conditions.

Example: Off-Center Load Diagram
How to Create an Off-Center Load Diagram
Though we explained above that an Off-Center Load Diagram shows the forming load limits, another way to express this would be, 'How much off-center loading can a press withstand (i.e., its allowable off-center load capacity)?'
Factors that can affect the allowable off-center load capacity of a press include the following.
① The Rated Capacity (Point Capacity) of the Press
Regardless of where the load center is (including any off-center loading), the forming load exerted on each point cannot exceed the capacity of that point.
② The Spacing Between the Points
The forming load exerted on the press slide is transmitted to the press frame, and in the case of a 2-point or 4-point press, the wider the point spacing (pitch) the better the press can withstand off-center loads.
In the case of a 1-point press, as a general rule we recommend avoiding any off-center loading.
③ Slide and Bed Deflection/Rigidity
The allowable off-center loading capacity is also dependent on press deflection and rigidity
④ Slide Guide Durability
Off-center loading will cause the slide to tilt while it is downstroking, and excessive tilting that could cause the slide guides to seize must be avoided.
Taking the above into account, a judgment is made as to how much slide tilt is acceptable during forming (i.e., to what extent parallelism should be maintained).
Off-center loading will also affect the dies and the accuracy of stamped products, and thus it is important to avoid off-center loads by evenly distributing the load balance as much as possible.