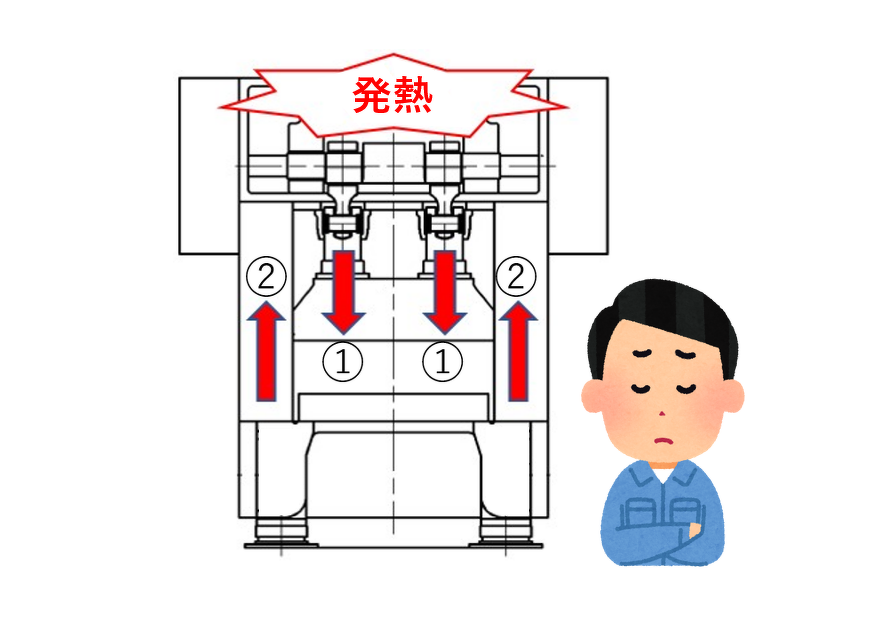
その不具合、スライドの下死点変位が原因かも?
スライドの下死点が安定しないと、どのような影響があるでしょうか?
まずは、製品精度への影響です。特に、潰し・刻印などの金型を使用する場合は、製品精度不良の原因になる場合があります。また潰し加工など、下死点変位のばらつきは金型応力増加につながり、金型寿命へ影響することもあります。
今回はそんなプレスの下死点を安定させるために、気をつけるべきポイントをお知らせします。
なぜ冬場や夏場は製品の品質が安定しない?
下のグラフは、プレス加工を開始してからの時間経過に伴う下死点位置を表したものです。
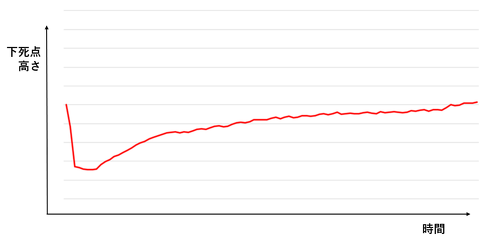
図1, プレス加工時の下死点変位
一般的にプレスは図1のとおり、打ち始めは下死点が下がっていき、30分ほど経過すると下死点が上がってきます。
このような傾向は、機械の発熱と室温の変化が影響しています。
なぜこのようなグラフになるのでしょうか?
プレスの運転を開始すると、回転部の摺動摩擦によって機械は発熱します。
すると、熱膨張によりクランクシャフト・コンロッド・プランジャーが伸びて、下死点が下がります。(下記図2と図3の①)
この熱膨張は30分ほどで安定しますが、その熱はフレームに伝わり、今度はフレームが伸びることにより下死点が相対的に上がってくるという現象が発生するのです。(下記図2と図3の②)
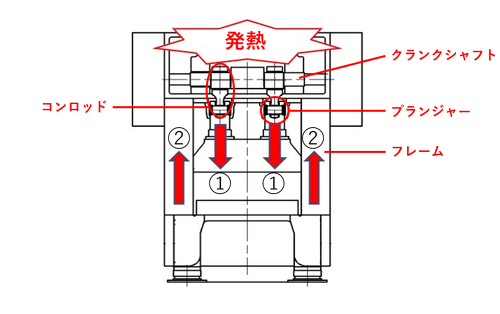
図2, プレス各部の熱膨張による影響
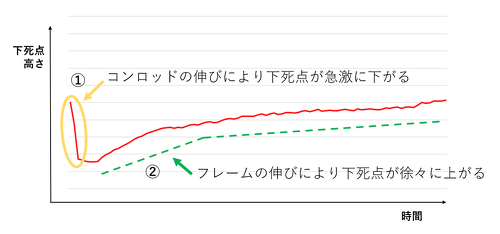
図3, プレス各部の熱膨張による下死点変位
さらに冬場は工場の暖房が朝から稼働して室温が上昇し、稼働が始まると潤滑油温も上昇して、フレームの伸びが促進される傾向があるのです。
逆に夏場でも製品精度が安定しない場合もあります。
下図は稼働中に工場の空調が入りクーラーで機械が冷えてしまい、フレームが縮んで下死点が相対的に下がってきた状態を表しています。
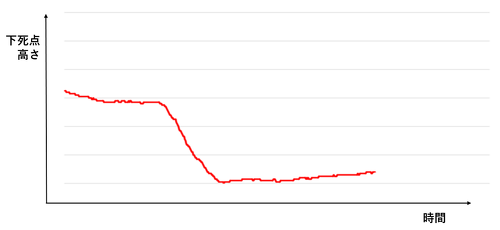
図4, 工場内クーラー稼動中の下死点変位測定
下死点を安定させるために
下死点を安定させるには、機械の運転中に室温が大きく変わらないようにすることが大切です。特に工場のエアコンの冷風・温風が機械に直接当たらないようにしましょう。またプリヒートの実施や油温コントロール装置の温度設定等により、下死点を安定させる方法も有効です。
室温を一定にしても下死点精度が安定しない場合は、定期的なメンテナンスによる静的精度維持や、偏心荷重の抑制等がされていないことが原因となっている場合もあります。
いかがでしたでしょうか?
ご不明な点がございましたら、ぜひアイダにご相談ください。